The traditional factory floor is on the cusp of a revolution. By strategically investing in emerging technologies, manufacturers can bridge the gap between the present and the “Factory of the Future,” a vision of intelligent automation, interconnected machines, and data-driven platforms. Enterprises are increasingly implementing various transformation initiatives to accelerate their strategy of creating the “Factory of the Future” by investing in the following three areas:
-
- Information technology (IT) and operational technology (OT) convergence: To gain access to real-time floor data and improve production monitoring and analytics
- Platform implementation: To enhance data accessibility and facilitate data consistency and transformation through manufacturing execution systems (MES), product life cycle management (PLM), and enterprise resource planning (ERP) implementations
- Industry 4.0 technologies: To improve data collection, analysis, sharing, and storage and enable remote assistance through AI, AR/VR, cloud computing, and IoT technologies
Figure 1 shows an overview of various transformation initiatives derived from our Manufacturing Digital Services 2024 Market Insights™.
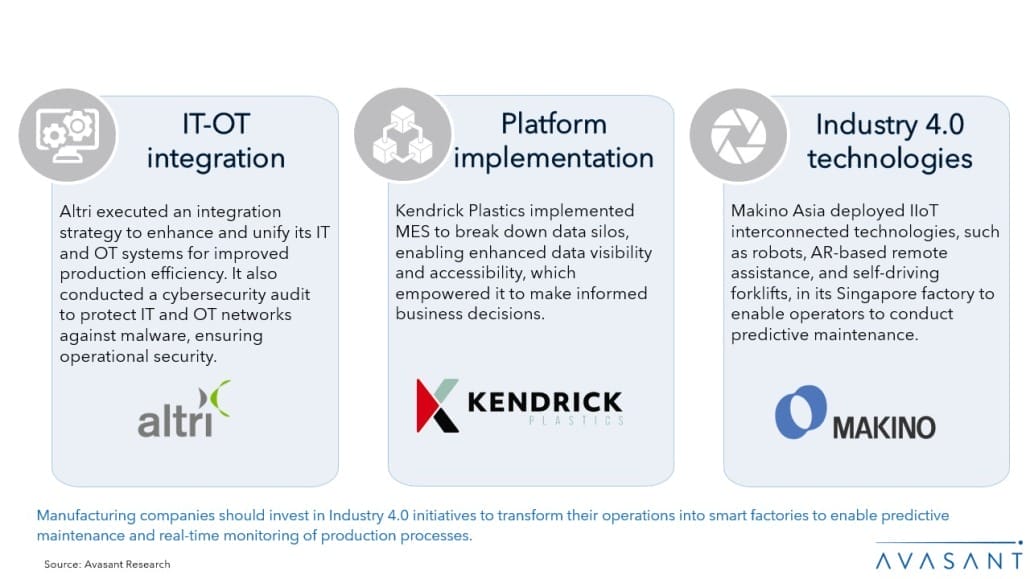
Figure 1: Various transformation initiatives adopted by manufacturing companies
Unlocking Next-gen Manufacturing with a Strategic Focus on IT/OT Convergence
Enterprises face a myriad of challenges while implementing IT/OT convergence and Industry 4.0 initiatives. IT and OT stacks are siloed, which leads to poor solution definition, deployment, and adoption. A lack of standardization across legacy systems and devices hinders communication and data flow between IT and OT systems, leading to interoperability issues. Finally, ensuring cybersecurity across the IT/OT landscape is a critical problem, as these systems are more vulnerable to cyberattacks.
At its recent analyst and advisor event in Hyderabad on June 27 and 28, President and Chief Business Officer of Hitachi Digital Services Santhosh Sreemushta highlighted the significance of IT/OT convergence, platform implementation, and Industry 4.0 initiatives for manufacturing enterprises. During the event, Sreemushta also described how Hitachi’s business has evolved over the years, starting as a core ERP service provider before its expansion toward enterprise cloud ERP and data services. Hitachi’s rebranding strategy from October 2023, which resulted in the spin-off of Hitachi Digital Services from Hitachi Vantara, was a move toward becoming an IT/OT system integrator to offer industrial IoT, enterprise cloud, and data services.
Various business leaders at the event demonstrated their focus on select industries and service domains via the One Hitachi operating model with key support from GlobalLogic for digital product engineering design and Hitachi Vantara for infrastructure services, highlighting key strengths in delivering enterprise-level manufacturing services through IoT convergence. They also emphasized their two core business lines: Green Energy & Mobility, which covers railways, high-speed rails, energy grids, and nuclear reactors, and Connective Industries, which covers elevators, buildings, and shop floors. These business lines outline the company’s growth sectors to facilitate IT/OT convergence for enterprises.
Unifying Business Processes with MES, PLM, and ERP Integration
In today’s competitive manufacturing landscape, integrating MES, PLM, and ERP is a beacon of innovation, driving efficiency and consistency across the board. This trifecta of technological solutions empowers manufacturers to harmonize their business processes, ensuring that data flows seamlessly and transforms into an accessible and actionable asset. By bridging the gaps between the shop floor and top floor, MES, PLM, and ERP integration fosters a unified digital ecosystem that is both agile and resilient, paving the way for manufacturers to excel in the digital age. As these platforms converge, they create a single source of truth, enabling decision-makers to orchestrate operations with unprecedented precision.
Bhusan Chand, senior vice president and global head of enterprise applications at Hitachi Digital Services, highlighted the importance of ERP implementations and ERP cloud migration to modernize the digital core of the manufacturing sector. He indicated that the company has developed a variety of platforms that facilitate the integration of business processes for manufacturers, with the core solutions including:
-
- Hitachi Application Reliability Centers (HARC): To design, deploy, and manage IT and OT applications on the cloud
- Smart Spaces & Video Insights (SSVI): To enable predictive infrastructure maintenance, improve safety, and streamline operations through video intelligence
Chand also illustrated how Hitachi has evolved its legacy ERP capabilities to support cloud, mobile, composable, and sustainable ERP practices, which are driven by AI, generative AI, ML, and RPA.
The Future of Factory Floors with Industry 4.0 Technologies
The traditional factory floors are undergoing a significant transformation driven by Industry 4.0, a revolution emphasizing the convergence of physical and digital technologies. At the heart of this change lies the Industrial Internet of Things (IIoT), a network of interconnected sensors and machines that capture real-time data from factory floors. These advancements facilitate predictive maintenance, optimize production lines, and enhance overall operational efficiency for manufacturers. By integrating IoT with advanced technologies such as AI, robotics, and big data analytics, smart manufacturing drives innovation in how products are designed, produced, and serviced. Figure 2 shows the enterprise adoption of Industry 4.0 technologies derived from our Manufacturing Digital Services 2024 Market Insights™.
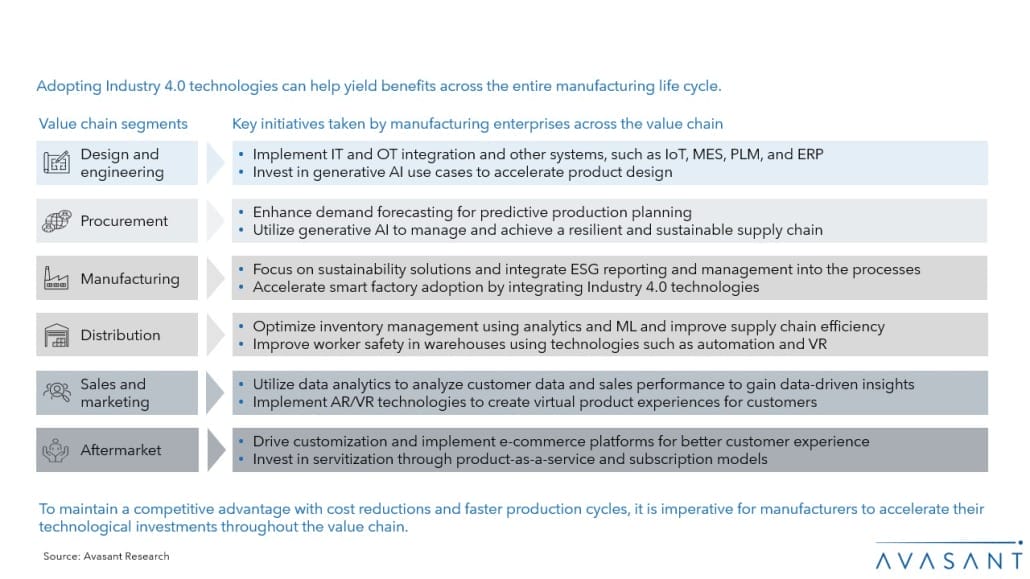
Figure 2: Adoption of Industry 4.0 technologies across the manufacturing life cycle
Vignesh Markandan, vice president of Manufacturing, Retail, and Consumer Products at Hitachi Digital Services, indicated that the company’s global digital services revenue was $20B in FY 2023, out of which the manufacturing sector revenue alone accounted for around $3.6B. He highlighted how the Omika Works lighthouse factory, Hitachi’s digital factory in Japan that leverages Industry 4.0 technologies, enables customers to reimagine the manufacturing of control systems for the metal, rail, and utility industries. He also illustrated how Hitachi Digital Services leverages the following Industry 4.0 technologies to drive growth and operational efficiency for manufacturers:
-
- AI/ML: To ensure worker safety at factories with industrial monitoring and automated inspection
- Data analytics: To drive production analytics, energy analytics, quality analytics, and supply chain analytics
- Digital twin: To predict and simulate procurement scenarios and identify vulnerable areas and ransomware attacks to facilitate cybersecurity innovation
Markandan also showcased a variety of case studies that illustrated the breadth and depth of its manufacturing portfolio. Some of them are listed below:
-
- Enabled efficient coal processing for a mining company by improving product traceability through AI-led industrial analytics. This resulted in cost savings of $500,000 and enhanced accuracy.
- Implemented the Hitachi Digital Factory Solution for a cable manufacturer to facilitate real-time monitoring and control over factory operations. It also utilized applied IoT technology to visualize the factory running status. This decreased operational fraud by 90%.
- Delivered an AI-based guided repair and proactive diagnostic solution for a transportation company with over 800 workshop facilities. This decreased the average wait time by 15 minutes per truck and enhanced maintenance scheduling.
The Way Forward
The “Factory of the Future” is not a distant vision but a tangible reality within the reach of manufacturing companies that embrace IT/OT convergence, platform implementation, and Industry 4.0 initiatives. By breaking down the silos between IT/OT, manufacturers can achieve seamless data flow and unleash the power of real-time insights. Through the strategic platform implementation of MES, PLM, and ERP systems, manufacturers can establish a cohesive data environment that boosts operational efficiency and drives innovation. Implementing IIoT solutions, advanced analytics, and intelligent automation unlocks new levels of efficiency, flexibility, and predictive maintenance.
The journey toward the “Factory of the Future” requires a strategic approach, investment in the right technologies, and workforce upskilling. However, the rewards are substantial—a competitive edge, reduced costs, and the ability to adapt to the ever-evolving demands of the global market. By taking the first step today, manufacturers can transform their operations and secure their position as leaders in the age of intelligent manufacturing.
By Dhanusha Ramakrishnan, Lead Analyst, and Gaurav Dewan, Research Director, Avasant Research